Cement Silo Manufacturers in Pune - Mahalaxmi Engineering Projects
We are the Top leadign Cement Silo Manufacturers in Pune Suppliers, Exporters of top Quality Cement Silos in Pune. Having decades of experience in serving solutions to the construction and cement industries, we are specialized in offering strong and reliable cement silos, designed according to the needs of our esteemed clients for various large-scale construction projects, cement storage, or bulk material handling purposes.
What is a Cement Silo?
A cement silo is a bulk material storage container, essentially a large, vertical container, specially designed to store bulk materials such as cement, fly ash, lime, sand, and other materials in construction, cement plants, or ready-mix concrete production. They provide the perfect solution for maintaining safety, dryness, and readiness of bulk materials in diverse industrial processes.
Cement silos play an important role in ensuring that cement remains within good conditions until it is required in production. They are engineered to face harsh environmental conditions, store cement effectively, and then discharge it when needed.
Types of Cement Silos We Manufacturer in Pune
At Mahalaxmi Engineering Projects, we offer a range of different cement silos to cater to various storage and handling needs. The types of cement silos we provides in Pune:
- Horizontal Cement Silos: These are most commonly offered in portable plants where mobility is a cardinal requirement. Horizontal cement silos provide space-saving compactness, making them easy to transport and install at various sites. These silos are typically applied for smaller production volumes or as an interim storage system.
- Vertical Cement Silos: Vertical cement silos are the most frequently used for large-scale cement storage. They are large, vertical containers designed to hold substantial volumes of cement and other bulk materials. Their vertical structure helps optimize space and is ideal for permanent cement storage at manufacturing plants and construction sites.
- Mobile Cement Silos: These are containerized and portable silos, offering flexibility and portability. Mobile cement silos are well-suited for temporary storage at construction sites or remote locations where cement is required in large volumes for a limited period of time.
- Self-Carrying Cement Silos: Self-carrying cement silos come with a built-in self-loading and unloading cement system. These silos are designed for continuous material handling, making them perfect for use in ready-mix concrete plants where high-efficiency operations are crucial.
Main Components of Cement Silo
Cement silos consist of several components working together to ensure the safe and efficient storage of cement. Below are the key Components of a Cement Silos:
- Silo Body: The main body of the silo, made from steel, holds the bulk material. The silo body is designed to withstand the pressure exerted by the stored material and the surrounding conditions.
- Cone or Hopper: The cone or hopper is positioned at the bottom of the silo to facilitate the easy discharge of the material. The cone directs the cement into the feed system, ensuring smooth flow out of the silo.
- Feed System: The feed system, which typically consists of a screw conveyor or an air slide, transfers the cement from the silo to the next processing or mixing stage. This system ensures efficient material handling and delivery.
- Level Indicators: Level indicators are installed to measure the amount of material stored in the silo. These sensors help determine when the silo is full or when the material level is low, providing valuable information for inventory management and silo operations.
- Dust Collection System: Cement is a fine powder that can create dust during storage and discharge. A dust collection system is essential for maintaining a clean environment and reducing the risk of contamination or environmental harm. It captures dust particles before they are released into the air.
- Safety Valves and Pressure Relief Systems: These components are crucial for ensuring the safe operation of the cement silo. They prevent excessive pressure buildup inside the silo, protecting it from potential damage during storage and material discharge.
- Access Ladders and Platforms: Access ladders and platforms are provided around the silo to ensure safe and easy maintenance. These ladders and platforms allow workers to access the top of the silo for inspection, cleaning, and maintenance activities.
- Discharge Gate: The discharge gate is the opening through which the cement or material is released from the silo. Depending on the design, the gate can be automatically controlled or manually operated, allowing for convenient material discharge.
Why Cement Silos are Important
Cement silos play a crucial role in the construction and manufacturing sectors. They offer several key benefits that make them essential for cement storage and handling:
- Efficient Cement Storage: Cement silos provide an organized and efficient storage solution for large quantities of cement. The silo design maximizes the available space, ensuring that cement is stored safely and efficiently, with minimal wastage or contamination.
- Lower Material Loss: Cement absorbs moisture and contaminants from the environment, which can degrade its quality. Storing cement in a silo protects it from environmental exposure, keeping the material in optimal condition at all times.
- Reduced Time on Transportation and Procurement: Cement silos allow cement to be stored on-site for quick access, improving production efficiency. This reduces the need for constant transportation and procurement, providing convenience for construction companies and cement manufacturers.
- Environmental Conservation: Cement silos come equipped with integrated dust collection systems to minimize dust emissions into the environment. This not only ensures adherence to environmental standards but also reduces risks to employees working with such machines.
- Customization: Cement silos can be tailored to specific storage needs, volumes, and industry requirements. They can be customized to handle various bulk powders, including lime and other materials.
- Cost-Effective: Cement silos are designed to be durable, low-maintenance, and efficient in operation, offering a cost-effective solution for long-term cement storage.
Applications of Cement Silos
Cement silos are widely used across various sectors that require cement or bulk material storage. Some of the main applications of cement silos include:
- Construction Industry: Cement silos are an essential part of the construction industry, where large quantities of cement are needed for mixing and pouring concrete. Construction companies can store substantial amounts of cement on-site, reducing the need for frequent deliveries and ensuring a consistent supply of material.
- Cement Manufacturing Plants: Cement plants use silos to store and discharge finished cement. The silos play a vital role in ensuring the safe storage of cement, ready for transportation to distributors or construction sites.
- Ready-Mix Plants: In ready-mix plants, cement silos are used to store cement while mixing the concrete. The silo ensures that cement is available on demand and is kept in optimal condition for mixing and production.
- Other Bulk Materials: Cement silos are also used for storing other types of bulk materials, such as lime, fly ash, or sand. They provide a safe and efficient storage solution for various industries dealing with powdery bulk materials.
Cement Silo Technical Information
A cement silo is an integral piece of equipment for any concrete production operation. Here are some technical details about cement silos:
Design Parameters:
- The roof of a steel silo should be designed as a conical shell with top and under tube, or truncated cone space truss structure.
- The steel cement storage silos are thread designed and applied galvanized steel sheet, which is the most popular technical process for steel silos in today's silo construction
Structure:
- The basic structure of a cement storage silo includes the building above the top of the silo, silo top, silo wall, silo bottom, supporting structure of the silo bottom, and foundation.
- The conveying equipment and maintenance platform of the building above the top of the silo should apply open steel channel structure.
- The bottom of a steel cement silo can apply a concrete structure or steel structure to support the silo body
Features:
- A cement silo is a closed storage silo for bulk material, including grain, cement, and fly ash. It is equipped with a material level system that can show the location and amount of the material.
- The hole breaking device can remove the firmness caused by long-term material deposition
Safety and Control:
- A manual lever controlled butterfly valve on the bottom of the silo cuts the material flow for screw conveyor servicing.
- Mix/Max level indicators send information to the batch computer when the amount is low or at its maximum.
- A safety valve prevents the silo from overpressure. The valve opens when the threshold pressure limit is reached.
- Aeration nozzles and airpipes ensure continuous flow of the material to the discharge area
Industries We Serve
Mining | Engineering | Automobile | Foundries | Dairy & Cattle Feed | Food & Beverages | Boiler Manufacturing | Ceramics & Tiles | Pharmaceuticals | Rubber, Glass | Robotic Welding & Welding Workshops
1. Cement Storage Silos: These are long cylindrical structures used for storing a variety of materials, including cement, fly ash, bentonite, and other bulk materials like sand, gravel, coal, and cement1. They are suitable for stationary applications and offer robust construction and low maintenance requirements, making them ideal for the containment of hazardous materials in industrial settings.
2. Horizontal Cement Silos: These silos are an option in projects where cranes are not available, anchoring is not possible, or there is limited space2. They can be made portable, making installation quick and easy, and are often used for construction sites, road works, and urban work operations. Horizontal silos can discharge materials through a cement auger and can be controlled by an electronic control panel and display system for easy operation.
3. Fly Ash Silos: Fly Ash Silos are used for storing fly ash and other bulk materials like cement, lime, and sand34. They are designed to store and discharge materials efficiently, making them suitable for concrete batching plants and other industrial applications where bulk materials need to be stored and retrieved
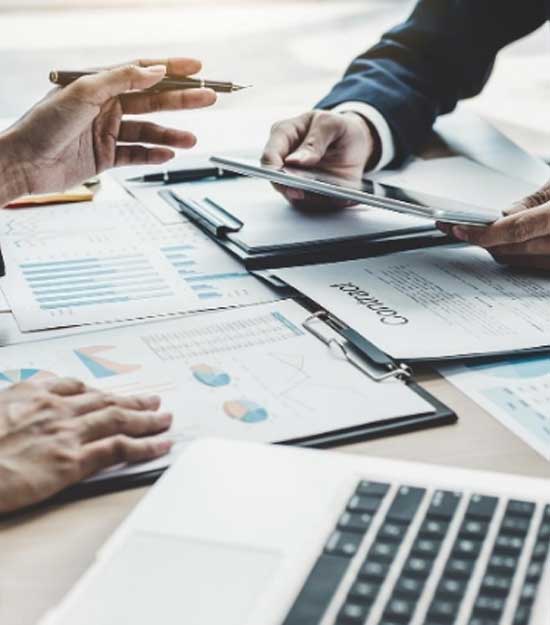