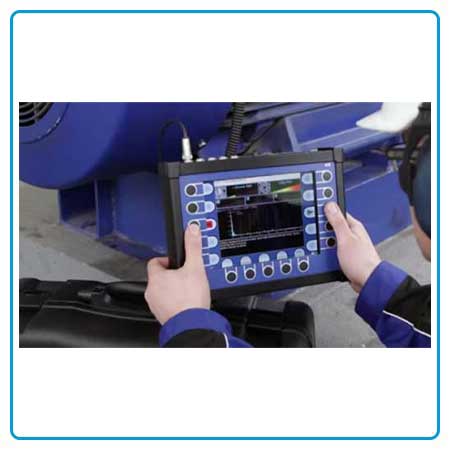
Vibration Analysis Services in India | Vibration Analysis Service Provider in Pune
Find the best vibration analysis and vibration monitoring service provider.
Mahalaxmi Engineering Project is a leading provider of vibration analysis services in India. We have been providing India’s best technicians for vibration analysis or monitoring and getting proper results to our clients since 2015.
Vibration Analysis Services are provided by professionals who specialize in using vibration analysis tools and techniques to diagnose the condition of machinery and identify potential issues before they lead to equipment failure.
We are vibration analysis service provider can help companies maintain their equipment in optimal condition, reduce maintenance costs, extend equipment lifespan, improve safety, and increase efficiency By monitoring and diagnosing potential issues.
Vibration analysis services are a technique used to monitor and diagnose the condition of machinery by analysing the vibration patterns and frequencies generated by the equipment during operation.
Our company can avoid costly downtime and repairs and ensure that their equipment operates efficiently and reliably.
It is a non-destructive testing method that can help identify potential problems with machinery before they lead to equipment failure.
List of Vibration Analysis Services:
- Vibration monitoring: This involves continuous monitoring of machinery using vibration sensors and data collectors to detect and diagnose any issues.
- Vibration analysis: This involves analysing the vibration data collected from sensors and data collectors using specialized software to identify potential issues such as imbalance, misalignment, resonance, loose or worn components, and electrical problems.
- Condition monitoring: This involves monitoring various parameters such as temperature, pressure, and vibration to identify any changes in equipment condition that may indicate potential issues.
- Balancing:This involves balancing rotating equipment such as motors and fans to reduce vibration levels and extend equipment lifespan.
- Alignment:This involves aligning machinery to ensure that the equipment operates efficiently and with minimal vibration.
- Predictive maintenance: This involves using vibration analysis and other techniques to predict when maintenance is required and proactively perform repairs or replacements to avoid equipment failure.
- Training and consulting: This involves providing training and consulting servicesto help organizations establish and maintain effective vibration analysis programs.
Vibration analysis can provide valuable insights into the condition of machinery and help identify various issues
Vibration analysis can be used in various industries, including manufacturing, power generation, aerospace, automotive, and more.
It can help reduce maintenance costs, increase equipment lifespan, and improve overall reliability and efficiency.
- Imbalance: An unbalanced machine can cause excessive vibration and lead to premature failure of bearings and other components.
- Misalignment: Misalignment of machinery can cause excessive vibration and wear on bearings and other components.
- Loose Or Worn Components: Loose or worn components can cause vibrations and lead to equipment failure if not addressed promptly.
- Resonance:Resonance occurs when the natural frequency of a machine matches the frequency of its operating environment. This can cause excessive vibrations and damage to the equipment.
- Electrical Issues:Electrical problems such as voltage fluctuations, phase imbalances, and grounding issues can cause vibrations and lead to equipment failure.
Benefits of Vibration Analysis/Monitoring
There are several benefits of using vibration analysis as a diagnostic tool for machinery, including:
- Early Detection Of Potential Problems: Vibration analysis can identify potential issues with machinery before they lead to equipment failure By detecting problems early, maintenance and repair can be scheduled and performed proactively, minimizing downtime and preventing costly repairs.
- Improved Equipment Reliability: Regular vibration analysis can help ensure that machinery is operating as it should, reducing the risk of unexpected breakdowns and unplanned downtime. This can lead to increased equipment reliability and improved productivity.
- Reduced Maintenance Costs: Vibration analysis can help identify minor issues before they become major problems, which can reduce the need for costly repairs or replacement of equipment. This can result in significant cost savings over time.
- Extended Equipment Lifespan: Regular vibration analysis can help identify and correct issues that can cause excessive wear and tear on machinery. By addressing these issues, the lifespan of the equipment can be extended, reducing the need for premature replacement.
- Improved Safety: Vibration analysis can help identify potential safety hazards, such as loose or worn components, before they cause accidents or equipment failure. By addressing these issues promptly, safety can be improved, and the risk of accidents reduced.
- Increased Efficiency: By identifying and addressing issues that can cause excessive vibration or other problems, vibration analysis can help improve the efficiency of machinery, leading to increased productivity and reduced energy costs.
Vibration Analysis Tools
Vibration analysis tools are instruments used to measure and analyze the vibrations of machinery to identify potential issues and diagnose the condition of the equipment.
We use list of tools for Vibration analyze and monitoring:
- Vibration sensors
- Data collectors
- Analytical software
- Balancing machines Alignment tools
- Spectral analysis tools
- Ultrasound equipment
ENQUIRY NOW